Where does one start with ubiquitous carbon black?
Let us start with the element. Carbon black is an allotropic form of carbon. It is a cousin to graphite and a poor relation to diamond. Its unique morphology and crystalline makeup help provide an enormous surface area per gram.
The actual history of carbon black and its uses could fill shelves. Here are just a few high spots:
The images of hands found on the walls of the Roucadour cave in Themines, France were made with a mixture containing carbon black approximately 24,000-28,000 years ago (1).
Much later, Guttenberg’s invention of movable type in 1450 created an ever-growing demand for carbon black for the ink business (2).
More recently, in 1879, “(Thomas) Edison began to abstractedly rolling between his fingers a piece of compressed lamp black (carbon black) until it became a slender thread…” (3)
By 1910, The Goodrich Tire Company started replacing white pigments in automotive tires with carbon black, thus increasing road wear by 100X and tensile strength by as much as 1008 percent (4).
The modern automobile culture could not exist without carbon black. Imagine having to discard tires every 450 miles because they had worn out.
It would be difficult to find a black product that does not contain some amount of carbon black (with the exception of food).
The Nature of Carbon Black
What is carbon black? Perhaps the best definition for a microscopist comes from ASTM D3053. It defines carbon black (CB) as “an engineered product, primarily composed of elemental carbon, obtained from the partial combustion or thermal decomposition of hydrocarbons existing as aggregates of aciniform morphology which are composed of spheroid primary particles…” (5).
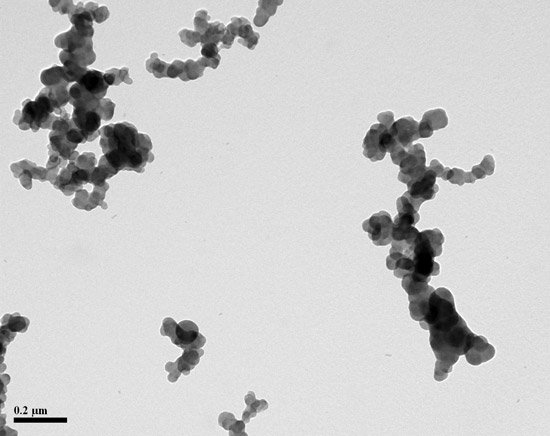
For those of us who do not speak standardese, carbon black is the result of partial combustion of organic material that results in agglomerates of smaller spheres of chiefly carbon. The important part of the definition is the “aciniform morphology which are composed of spheroid primary particles…” In other words, carbon black particles looks like small clusters of grapes.
It is tempting to consider carbon black the only nanomaterial which was used 27,000 years ago as well as by materials scientists today. Sadly, the current definition of nanomaterial is size based and tops out at 100 nm (500 nm Europe) in length. While most primary particles are smaller than 100 nm, the agglomerations are larger and excluded by definition (6); perhaps future technology will produce a true nano size carbon black.
Down and Dirty
Carbon black is not the only black pigment used in products. Bone black, made from the pyrolysis of bones, is another example. This pigment is found in a range of products where low toxicity, specific shades of black, and lack of reinforcement are desired. Bone black can be found in artists’ paints and printers’ ink (7).
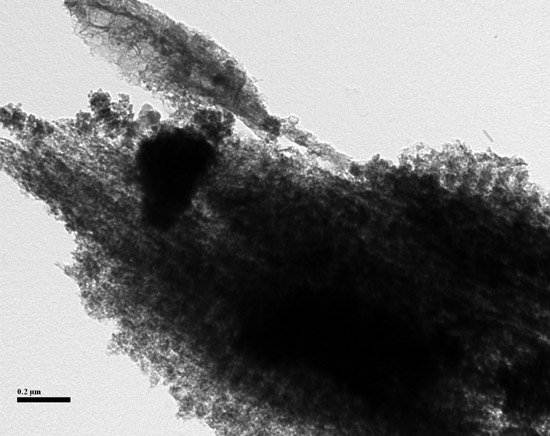
The structure of the particles appears to be unique and its composition of carbon and calcium phosphate makes the material easy to identify. Despite this, I have seen it only as a reference material, never in a commercial polymeric product; one reason for this could be cost.
There is another product which has many of the same properties as that of bone black; namely, Austin Black (8).
Austin Black is bituminous coal dust. It has a specific gravity of 1.3 g/cm3 as compared to 1.8 g/cm3 for carbon black, and 2.6 g/cm3 to 2.8 g/cm3 of some mineral fillers, making it a low cost filler for rubber and plastic products. It also has slightly different tonal shades of black as compared to other black pigments. Products such as bus flooring, car mats, and vibration mats, which require very little reinforcing, can benefit from Austin Black.
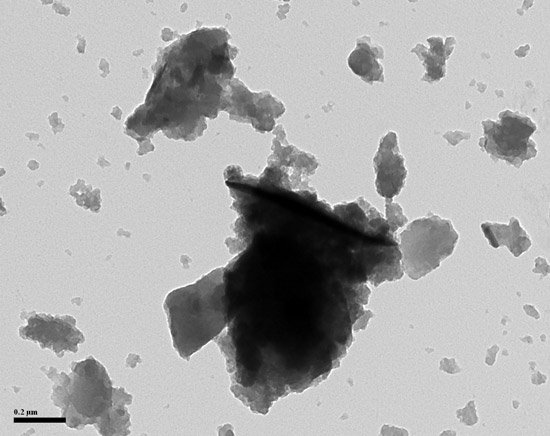
Austin Black does not resemble either carbon black or bone black. Its amorphous shape and lack of identifying characteristics make Austin Black almost impossible to identify in products. Polymer formulations containing halogens or nitrogen form a black char during carbon black recovery that resembles Austin Black. Very often Austin black is identified by ruling out char-forming polymers and not finding any carbon black in the recovered black-colored ash. To paraphrase Sherlock Holmes, after everything reasonable is ruled out, what remains, no matter how improbable, is the likely answer.
CB Classification
The original carbon black classifications (9) were based on the manufacturing method and a vague description of the CB’s use.
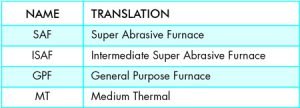
Carbon black has a wide range of physical properties depending on the manufacturing process, and manufacturers soon had the market filled with conflicting names and claims. Consensus standards began to emerge in 1954 with the formation of American Society for Testing and Materials (ASTM) Committee D24 on Carbon Black. D24 still remains one of the more active ASTM committees.
ASTM D24 originally imposed order on the carbon black market by the creation of four-digit codes still in use today (10). The first digit implied whether the CB increased the vulcanization rate of a standard formula or not. Today we see only the normal grades, or “N”, and not the “S” for slow. The second digit describes the average size range of the ‘grapes’, or primary particles. What better way to measure these particles than by using a transmission electron microscope (TEM)?
N100 CB. N300 CB. N700 CB.
Most carbon blacks were classified as an N100 to N900 type based on average size. The last two digits were assigned numbers to create brand separation based on oil absorption and iodine number.
While primary particle size is an important component, it is outweighed by surface area. Manufacturers used to provide both average particle size and surface area to assist rubber compounders in optimizing the cost/performance ratio of their product.
A modern view of how CB reinforces polymers involves molecular interaction at its surface and the polymer macromolecule. In my opinion, these factors and the increasing cost of owning and operating a TEM caused ASTM in 1996 to change CB grading criteria from average primary particle to surface area as measured by BET Nitrogen Surface Area. Values for both historic average size and the current surface area limits can be found in Table Two. A more intimate look at how carbon black’s properties are utilized in rubber compounding is beyond this paper.
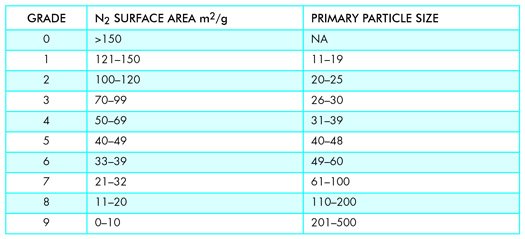
Modern manufacturing can produce a single grade of carbon black in multi-train-car lots by running continuously for months on end, during which QC samples must be taken on a rigorous schedule. The number of samples needing analysis from all stages of production from combustion, quenching, cooling, pelletizing, drying, and bagging can overwhelm the production lab. For carbon black manufacturers, N2 surface area is faster, cheaper, and more economical. But for product reverse engineering or failure analysis, N2 surface area is a high dive into an empty pool.
Why? Two reasons:
- BET N2 surface area measurements require a minimum surface area, not sample weight. This calls for recovering a large amount of CB and an even larger polymer sample to start with.
- The interaction between the CB’s surface area and the polymer is not reversible, resulting in an erroneous low surface area (11).
Once again, it is time for the TEM to shine.
Recovering Carbon Black
Like so many other things, carbon black recovery is a multi-step process.
Rubber products contain other fillers in addition to carbon black—clays, metal oxides of zinc, magnesium, titanium, and calcium are but a few. Fortunately, based on morphology we can just measure the primary particle of the aciniform morphology and ignore the rest.
This process works fine until we wash up on the rocks of silica. Silica is often called the white carbon black for good reason. Both precipitated and fumed silica have aciniform morphology. Silica can be mistaken for carbon black, and its measurement throws off the average value. If you measure 200 particles, every two particles of silica measured by mistake is one percent of your total. A mistake common to most manual particle sizers is preferentially measuring the larger and easier-to-see particles. The analyst must strive to count a statistically representative number of small to tiny particles as well as the easy-to-measure particles to obtain an average truly representative of the sample. This is a potential source of error. Silica requires another decision on the part of the analyst and introduces another source of error.
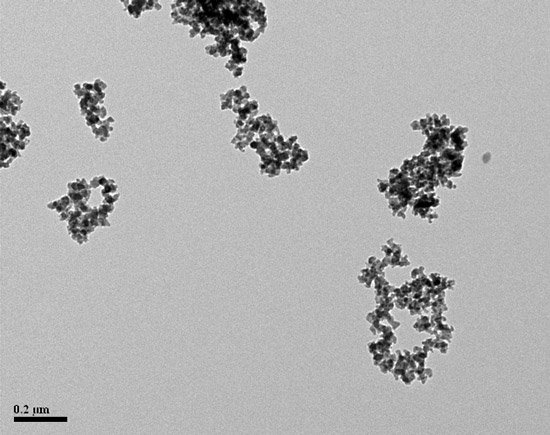
To insure the results reflect the best possible interpretation of the CB present, the microscopist is forced to draw on their experience and expertise to decide what is and what is not silica for every particle they measure.
There is an easier way.
ASTM D3849 “Carbon Black – Morphological characterization of Carbon Black Using Electron Microscopy” tells us how to recover and prepare carbon black samples for TEM analysis.
Like any good cook, I follow the recipe so far and then depart based on experience. The procedure calls for rubber filled with carbon black to be pyrolized in an inert atmosphere at the polymer decomposition temperature. I have used both a nitrogen atmosphere and vacuum, but the key in either case is to exclude oxygen. Of the two options, I prefer vacuum as I think the vacuum produces a cleaner, easier to disperse carbon black.
Hold the sample at 550°C for one hour in an inert atmosphere/vacuum and cool to room temperature while protected from oxygen.
ASTM D3849 section 7.3.3 states “…containing 5% or more silica typically results in higher sintered aggregate dispersions with agglomerated silica. Advanced techniques for the removal of the silica must be employed to get reliable results.”
What those techniques are is not revealed.
Following pyrolizing, I simmer a portion of each sample in a platinum crucible with 7 ml of 50 percent hydrofluoric acid, HF. I leave the time open-ended. I want all of the silica to react and give it the time to do so. You need to perform this operation in a fume hood with good ventilation, and utilize all safety precautions such as the use of nitrile gloves, eye protection, and of course, do not pipette by mouth.
The HF reacts with silica and other mineral fillers. Chemistry indicates the silica forms hexafluorosilicic acid and tetrafluorosilane, both of which sublime. After HF treatment the confusing silica morphology is gone, leaving only the unique carbon black morphology.

I run all of my samples through this regimen, especially the recovered carbon black from tire recyclers. Where you and I might see piles of worn out tires, failed truck tires and conveyor belts, carbon black recyclers see gold. Unfortunately, every component in a tire, tread stock, belt stock, inner liner, apex, and side wall stock has a different formulation. No matter how the recycler tries, his product will contain numerous N-number carbon blacks, clay, silica, TiO2, Ca, Mg, and Zn oxides as well as mica, metallic zinc, and iron oxides.
Not all recyclers remove all the organic portions. I contend that even recovered carbon black samples need to be pyrolized and acid washed to give good dispersions.
After the acid treatment, I follow ASTM D3849. I grind the treated sample in chloroform using a small agate mortar and pestle (tetrahydrofuran, THF, is the preferred solvent, but it gives me headaches); transfer to a small corked test tube, and ultrasonicate the chloroform/carbon black mixture for 10 to 30 minutes.
Place at least two TEM grids on a filter paper lined Petri dish, carbon film side up. Wet the paper with the same solvent used to disperse the carbon black, and lay down two to three carbon coated TEM grids. Transfer a micro drop to a carbon film TEM grid using a 20 µl microcapillary pipette. The solvent damped filter paper will provide enough surface tension to hold the grids down during transfer.
With practice you will find the right dilution that will provide a sample with sufficient particle density. It is poor technique to count all 200 particles (or as many as you think are statistically representative) from one field, but you also want to avoid having to examine every field to find enough carbon black to count.
TEM Examination
The TEM was never intended to be used for measurements, but we all do it. Maximize the repeatability as much as you can. Make sure the sample is at the eucentric position and the lenses are free from electrical hysteresis. The column should be aligned and images stigmated. I selected a TEM magnification that does not exclude either the very large or the very small. Try to select a magnification that will work over the entire particle size range from 7 nm to 300 nm. I would also suggest establishing an image library of known carbon blacks at the same magnification.
Blends and Averages
This is the intersection of science and art. Many compounders will blend carbon black types to maximize the properties desired in the rubber formulation. A formulation might require an N200 for abrasion resistance and N600 to resist compression set. The recovered carbon black will contain both. A simple average will mislead the analyst depending on the ratio of the different carbon blacks used and counted. It is not uncommon to find that most blends average to a N400; it is in the middle of the scale.
Examination of your images and the comparison of those to pure N-numbers standards may suggest it could be a blend of two or more carbon blacks. I have seen formulations containing three carbon black types, but they are the rare oddity. Since CB is now typed by BET nitrogen surface area, manufacturers can blend CB types to achieve desired values and the N number may have quite a size range.
Compounders maximize physical properties by using blends of polymers and of carbon blacks. As a microscopist we are attempting not to read the compounder’s mind, but to provide an honest estimate of what carbon black or blacks are present.
Here is the final exam: The picture below contains carbon black that you recovered from rubber stock. Most of the TEM fields contain particles like these. Are the smaller particles silica or carbon black?
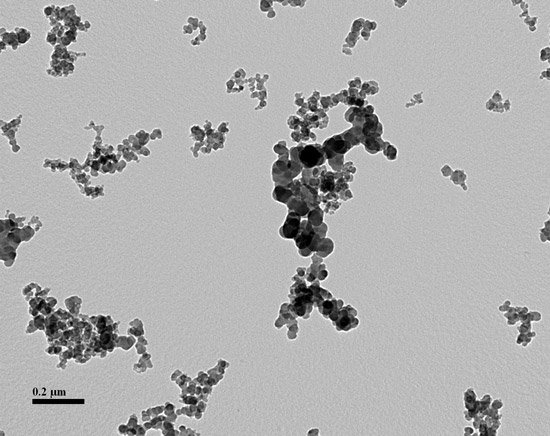